Pier
The pier is a reinforced concrete structure featuring a platform upheld by steel profiles, designed to accommodate the telescope and enclosure. It serves as a foundation for the telescope structure, enclosure, and associated auxiliary equipment, facilitated through the maintenance platform and the Coudé Room, which encompasses all instruments of the EST. Moreover, the pier serves as a conduit for access, connecting the ground floor to the Coudé Rooms and the enclosure floor.
The core structure of the pier consists of reinforced concrete, featuring structural walls with a thickness of 0.7 meters. These walls bear the weight of the telescope, telescope platform, enclosure, and the pier itself. Additionally, the pier serves as a thermal insulator for the interior and Coudé Rooms. The bottom section of the pier takes on a cylindrical shape, accommodating the Coudé Room. The external diameter of this cylindrical segment measures 25.3 meters.
Above the Coudé Room, the pier transitions into a truncated cone shape, designed to minimize disruptions in airflow. It then returns to a cylindrical form, optimizing the space within the enclosure volume. This configuration culminates in a crowning beam with a diameter of 8.4 meters. This shape has been meticulously chosen to effectively distribute the telescope's loads to the exterior of the pier.
The principal structure has an overall height of 32 meters and is comprised of a concrete volume totaling 2525 cubic meters.
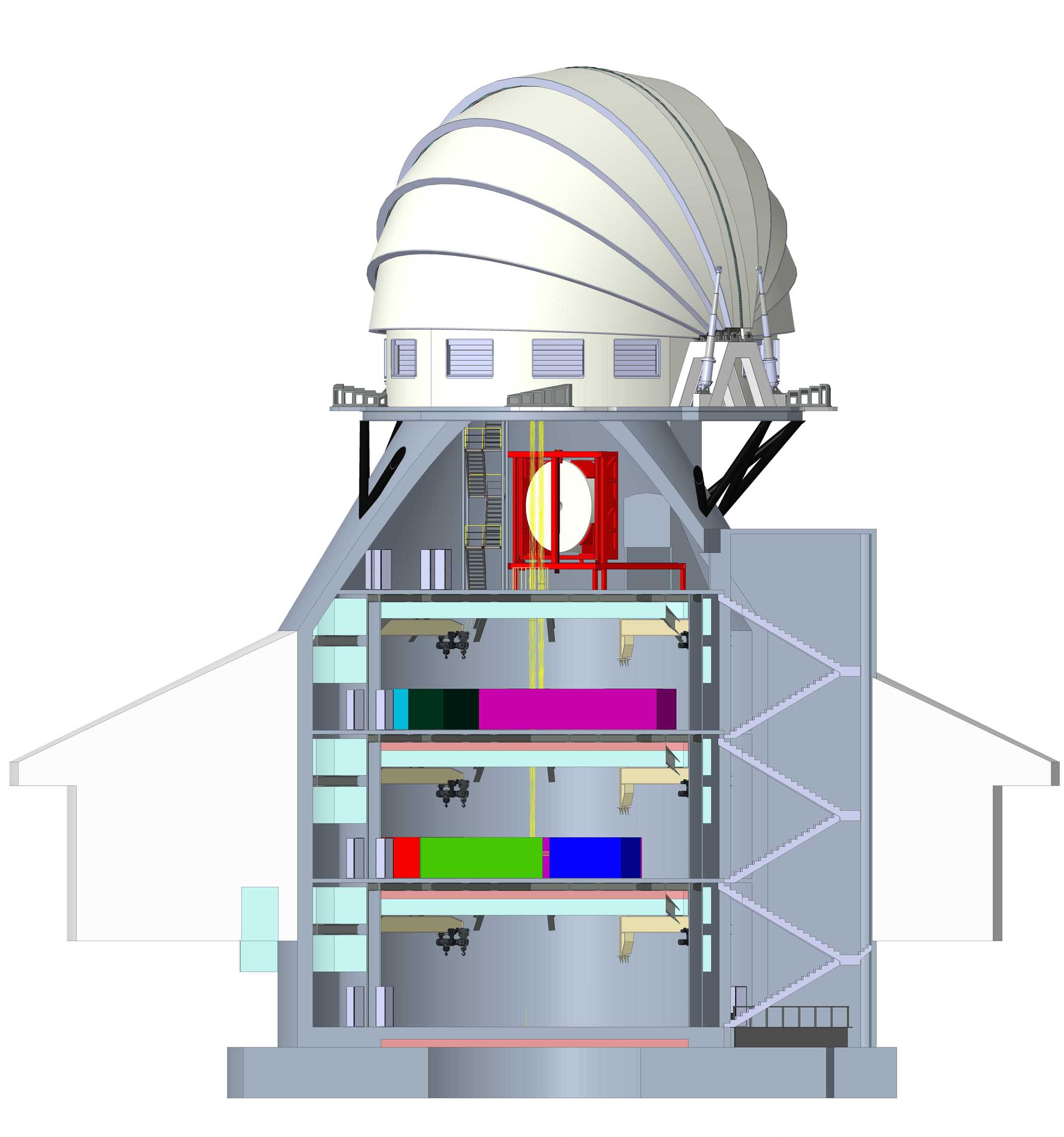
EST Pier